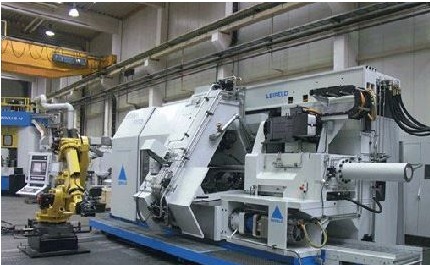
Spin forming is a special method of metal plastic forming. The principle of spin forming is to fix the blank on the die. The die rotates with the blank at a high speed. The outer roller exerts a great pressure on the blank, causing the metal blank to deform and finally form. Parts that match the shape of the mold.
Spinning is divided into ordinary spinning and strong spinning. Ordinary spinning means that the shape of the blank changes during the forming process, and the thickness of the blank does not change. Ordinary spinning is of very early origin and is most widely used in civil applications such as utensils, cutlery, and parts with low precision. Strong spinning is not only a change in the shape of a blank during the forming process, but also a change in thickness. Thinning, the volume of the blank is not changed during the spinning process, and the thinned blank material increases the height of the part. Strong spinning is a non-cutting process and there is no loss of material during processing.
As a new technology in modern plastic processing, strong spinning is applied most widely and widely in various fields of the defense industry. Strong spinning has obvious advantages in the production of thin-walled high-precision rotary components:
After strong spinning, the strength and hardness of the material are increased by about 35%~45% than that of the base metal. Therefore, in the aerospace field, the strong spinning pressure can effectively reduce the design wall thickness of the part and reduce the weight, and its fatigue performance can also be significant. Increased; Strong spinning pressure on the thick-skin blank point by point to apply high pressure to thin deformation, the flow of metal fiber material is protected, making the part of the fatigue performance has been improved; strong spinning pressure is an integral forming technology, forming parts do not Busbar welds, so the overall performance of parts, especially the fatigue life can be significantly improved; strong spinning without cutting and a simple forming mold reduces production costs, shorten the manufacturing cycle of parts; strong spinning in a forming process The billet can be thinned by 60% or more. Due to the large reduction rate, the strong spinning can effectively inspect the metallurgical defects in the base metal; the super-wide plate can be produced and processed by the strong spinning pressure; the dimensional tolerance of the strong spinning parts And the tolerance of shape and position is small, the precision is very high, even higher than mechanical processing.
Based on the above advantages, strong spinning technology has been widely used in the manufacture of parts for the chemical industry, nuclear industry, shipbuilding industry, weapons, aerospace, and especially aircraft and aircraft engines. For example, some common large-scale pressure vessels for chemical industry, ships, and boilers have certain requirements for internal pressure due to the existence of busbar welds. If the intermediate cylinder section is formed by the spin forming process, the weakest link of the pressure vessel, the straight weld seam, can be eliminated. If strong spinning is used, the overall strength of the cylindrical part is increased by 12% to 25% than that of the base metal, which greatly improves the safety and reliability of such pressure vessels, and the mold is simple to manufacture, the manufacturing cycle is short, and the processing cost is low. This method of raising the pressure pressure of the pressure vessel cannot be achieved by any other machining process. If such pressure vessels are used in the aerospace field, the wall thickness of the vessels can be greatly reduced under the same pressure, thereby reducing the weight of the components and reducing the fuel consumption and increasing the range.
In addition to the traditional metal materials such as carbon steel, aluminum and its alloys, copper and its alloys, and stainless steel, strong spinning forming materials include spinning of some special materials developed in recent years, such as high-strength steel and ultra-high strength. Spinning of steel, titanium and titanium alloys, superalloys, tungsten, molybdenum, niobium, and their alloys, it can be said that in the field of metal plastic forming, the types of metal materials that can be spin-formed are the most widely used.
More and more components on aircrafts and aircraft engines use hard-to-deform materials such as titanium alloys and high-temperature alloys. These components have complex profiles, such as hyperbola, parabola, and double taper, and they all have high requirements for wall thickness tolerance, diameter tolerance, roundness, and straightness. For these parts, the main process at present is forging after machining. Material utilization can only reach 3%, a lot of valuable materials are turned into iron filings, and destroy the metal fiber flow itself. The use of strong spinning technology, can make the spin-casting parts of the material after the grain refinement, strength, anti-fatigue performance is improved, so that the wall thickness of the component is reduced, the reliability of parts is greatly improved.
The application of spinning technology is more and more extensive, and the requirements for spinning presses are getting higher and higher, especially the spinning equipment with large rotating diameter, high thrust, high precision and high automation. The foreign strong spinning equipment has been serialized and continues to develop in the direction of large-scale, multi-purpose and high automation. With the development of computer technology, the spinning machine control system has also developed. Roller feed has fully developed to CNC, spindle speed has progressed from grade to gradeless, and it has developed into multi-spindle swivel spinning machine. The television monitoring system and wall thickness ultrasonic automatic measuring device required for processing large-diameter parts have also been applied to spinning machines.
As far as the level of spinning technology is concerned, there is not much difference between China and foreign advanced technologies. Although there is a gap between the degree of automation and reliability of spinning equipment and foreign advanced technologies, this gap is getting smaller and smaller. In recent years, China has made breakthroughs in the research and development of large spinning equipment. As the earliest research unit, AVIC Manufacturing has developed spinning process and spinning equipment for nearly 50 years. In the development of spinning process, in spinning parts of special-shaped parts and special materials, the institute has been leading in the country.
Recently, the largest numerical control vertical spinning machine in Asia developed by the Institute of Aerospace for a space company has completed process acceptance. The equipment is a vertical three-wheel structure, the equipment itself weighs 600 tons, a single rotating wheel thrust is 100 tons, the machine tool rotating diameter is 2.6 meters, and the large-sized tubular parts capable of spinning 2.6 meters in diameter and 3.5 meters in height can be Ultra-high-strength steel with a thickness of 35 mm is rolled to a thickness of 2 mm. After spin-pressing, the wall thickness of the cylinder reaches an accuracy of one hairline, which is higher than that of mechanical processing. The equipment has three unique features of spinning pressure self-regulating self-balancing, synchronous feed and wrong distance spinning, etc., with the characteristics of intelligent spinning, the overall technology has reached the international advanced level.
Spin forming applications are becoming more and more widespread. Spinning technology can solve the major bottleneck problem that restricts China's manufacturing industry and military industry. Embodying the combination of military and civilian forces and the integration of military personnel into civilians is of great strategic significance in safeguarding national security and enhancing comprehensive national strength. With the development of China’s national economy and military industry, this traditional process of spin forming will inevitably rejuvenate and play an increasingly important role.
Popular Mesh Belt Co., Ltd. , http://www.nspolyesterfabric.com