I. INTRODUCTION At present, domestic large-scale thermal power plants and units basically realize the DCS control system, and a wave of “DCS†is sweeping various types of power plants and units. On the basis of the control of power plants and crew computers, more and more power plants have begun to pay attention to operational economic problems. Optimizing operations has gradually become an important part of power plant operation and management.
Performance calculation is an important function of the DCS system, but the traditional performance calculation function is mainly for production management services, and the real-time performance requirements are not high (usually ten minutes or more), and in addition to the performance calculation function In addition, there is no performance analysis and operation guidance function. Obviously, this kind of performance calculation function has very limited guidance for optimizing operation.
With the rapid development of computer technology, based on the new DCS system platform (such as Xinhua's XDPS-400 system), it is possible to realize real-time online calculation of performance calculation and more complex analysis and calculation functions. The performance analysis system developed on the basis of the real-time online performance calculation function, combined with the DCS system, will be able to make full use of the potential of the DCS system and make the DCS system play a role in optimizing the operation.
Xinhua XPA is a performance-based analysis system for large-scale thermal power units. It is an operation-oriented software system developed by Xinhua on the basis of XDPS. The system provides three analysis and diagnostic functions: performance calculation, energy loss analysis, fault diagnosis and operation guidance. It is an effective tool for power plant auxiliary optimization and optimization management.
Second, XPAS performance calculations.
DCS system configuration XPAS performance calculation software can provide long-term changes in performance values ​​and unit performance of the unit and the main auxiliary equipment. By using this function, the operating personnel and management personnel will be able to know the performance indicators of the current operation of the unit; through the DCS report function and historical record function, the management personnel can know the average operating performance indicators and the long-term variation trend of the unit performance of each running team. Operation assessment and equipment maintenance provide the basis. The performance calculation function provides a number of performance indicators for units and major equipment that cannot be directly measured:
1. Unit performance, such as unit heat consumption rate, steam consumption rate, cycle thermal efficiency, plant electricity consumption rate, power generation coal consumption, power supply coal consumption.
2. Boiler performance such as combustion efficiency, smoke heat loss, and other combustion losses.
Air precipitator performance such as air precipitator leakage rate, flue gas side efficiency, air side efficiency.
4. Turbine performance such as cylinder steam intake flow, exhaust flow, efficiency, output internal work, low pressure cylinder exhaust dryness, low pressure cylinder exhaust steam enthalpy and so on.
5. Small machine and feed water pump performance such as small machine efficiency, feed pump efficiency, feedwater pump water soaring and so on.
6. Heater performance such as steam inlet flow, end-to-end pressure, pressure loss in the extraction pipeline, surge in water supply, etc.
7. The performance of deaerator such as steam inlet flow, pressure loss and overcooling degree of extraction pipeline.
8. Condenser performance such as undercooling, heat transfer, temperature, circulating water temperature rise, heat transfer coefficient, cleanliness coefficient, circulating water flow (calculated by thermal balance method).
III. XPAS's energy loss analysis function XPAS's performance calculation function provides the current performance value of the unit, but the operation and management personnel can not know the best possible performance index under the premise of the unit's current power generation index, nor do they know the parameters. The contribution of the deviation to the deviation of the performance index (the difference between the best performance index and the current performance index) (called energy loss), and the optimization of the operation and the arrangement of the inspection and repair still cannot be started. The loss analysis function tries to solve this problem. It is software developed to optimize the operation and optimize equipment overhaul. First, the energy loss analysis module of the performance analysis system calculates the current working condition of the unit (this condition is the best performance condition of the unit under the same conditions as the current total feedwater flow of the unit); then the current operating conditions of the unit will be Compared with this standard operating condition, the equivalent enthalpy drop theory is used to calculate the contribution of the specific parameter deviation to the deviation of the performance index (energy loss caused by the parameter deviation), so that the operating personnel can carry out targeted adjustments and the management personnel can have Targeted inspection and maintenance to achieve optimal operation and optimize equipment maintenance.
The loss analysis project has the following content:
1. Energy loss caused by main steam pressure deviation;
2. The energy loss caused by deviation of main steam temperature;
3. The energy loss caused by the reheat steam temperature deviation;
4. Energy loss caused by superheater spray water cooling;
5. Energy loss caused by reheater spray water cooling;
6. The energy loss caused by the increase in heater terminal difference (each heater);
7. Energy loss caused by increased heat dissipation in the pipeline (each extraction pipeline, main steam pipeline, reheat steam pipeline, main water supply pipeline);
8. Energy loss caused by increase in pipeline pressure loss (each extraction pipeline, main steam pipeline, reheat steam pipeline, main water supply pipeline);
9. Condenser vacuum to reduce the energy loss caused by;
10. The energy loss caused by the increase in condenser supercooling;
IV. XPAS's fault diagnosis and operation guidance XPAS energy loss analysis module can quantitatively calculate the energy loss caused by various parameter deviations in real time, but the energy loss may be caused by the operation reasons, or it may be due to the equipment. Caused by. When the unit is running, changes in parameters may be a sign of some type of accident. How to distinguish between the energy loss caused by the operation or the energy loss caused by the device? How to reduce the energy loss through operation adjustment? What are the possible causes of energy loss caused by the equipment? What kind of accident may be a precursor to changing parameters? What measures should be taken after fault location? This module attempts to answer these questions. This module contains the following:
1. Operation guidance and equipment status diagnosis guide. The possible causes and solutions to increase the energy loss caused by the parameter deviation are given.
2. Fault prediction, fault diagnosis and troubleshooting instructions. The equipment failures characterized by the parameter changes may be discovered earlier by experienced operators. However, due to the many parameters that need to be monitored during the operation of the unit, or due to the negligence of the operating personnel, it may not be possible to detect the fault early. Using computer software to assist in fault prediction and fault diagnosis is a powerful tool to solve this problem. The computer software can also provide guidance on troubleshooting and play the role of an “operational expert†to reduce the labor intensity of a truly operational expert, which is beyond the reach of the average manpower.
This module uses the principles of an expert system and absorbs knowledge of many power plant operation experts. In order to make the software more “humanized†and more in line with the actual conditions of the specific unit, the relevant contents of the furnace, machine and electricity operation procedures of the specific unit can be incorporated into the software, and the man-machine interface can be designed according to the opinions of the specific power plant experts. .
V. Advantages of the XPAS system and the differences with the MIS system 1. The XPAS system is an operating software system, which is different from the development orientation of the MIS system for management;
2. The XPAS system is a software system developed on the basis of XDPS system of Xinhua Company. The analysis and calculation results can be accessed on all DCS operators' stations, directly playing the role of guiding operation; MIS system can only obtain data from the DCS system. Can not directly guide the operation.
3. XPAS system inherits all the advantages of Xinhua XDPS system software (real-time, flexibility, easy learning, independent intellectual property rights), applicable to Xinhua XDPS DCS system, can also be adapted to other DCS systems.
V. Operating Hardware Environment 1. The operation of the complete software system requires adding a performance computing station to the DCS system network, as shown in Figure 1. The configuration of the performance computing station is the same as that of the historical station.
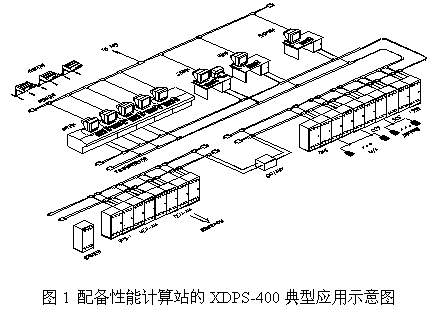
2. The separate performance calculation function software can also be run using the engineer station of the DCS system.
Note: XPAS is the abbreviation for English XINHUAPERFORMANCE ANASYSIS SYSTEM
Threaded Rod
Acme Threaded Rod,Screw Rod,Hardware Series
Shandong Shanglong Economic and Trade Corporation Ltd , http://www.chthreadedrod.com