The relocation and upgrading project of Datong Gear Co., Ltd. meticulously built by China National Heavy Duty Truck Group has been completed and settled in the Equipment Manufacturing Park of Datong City, Shanxi Province. The total investment of the new project is 1.2 billion yuan, and the first phase of land acquisition is 917.6 mu, mainly used for the whole Relocation, equipment manufacturing, and product quality have greatly improved.
Datooth's overall relocation and upgrading project is a strategic plan for Sinopec to build an advantageous industrial chain and implement industrial optimization and upgrading. It is also a good starting point for strategic cooperation between China National Heavy Duty Truck Group and Datong City. After the company moved into the new factory area, the gearbox production line was all in accordance with the lean production layout. With logistics as the main line, the production workshops were arranged according to the process flow sequence, and the overall planning of the logistics system was carried out, with the flow of people and information. Continuous, smooth, efficient, and uninterrupted logistics system, U-shaped layout of the production line, streamlined production, a large modern manufacturing company before the world.
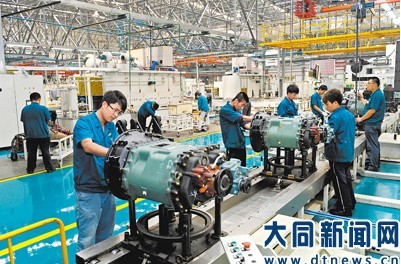
In the past two years, the production and operation of big teeth have been showing strong development momentum. Especially in 2010, all business indicators of the company have reached historical highs. Despite these achievements, corporate decision makers have not been immersed in excessive joy. It began to investigate, analyze and forecast the market, position new products to fill market gaps and broad prospects for development, so that new product development is always ahead of schedule. Due to many reasons such as the hot market in 2010, the domestic and foreign markets were relatively saturated in 2011. At this time, the mass production of new products just became a powerful breakthrough for the company.
The speed with which new products are developed is critical, and it largely determines the market share. After joining China National Heavy Duty Truck Group, Grand Teeth has made extraordinary efforts in new product development. Through technological innovation and technology sharing, product R&D capabilities have been comprehensively improved, and the time from new product development to mass production has been greatly reduced.
It is understood that during the research and development of new products, the R&D personnel, workshop technicians, production management personnel, and on-site operators are all on site, and any improvements in the discovered processes, tooling, etc. will be made at any time. The final assembly shop is the final process of the finished product. For the new product R&D work, the employees at each stage are all stepping forward and seamlessly connected. As long as there is a problem in research and development, we will not give up if we do not resolve it.
The 1900-million full synchronizer gearbox independently developed by Big Tooth Co., Ltd. fills a gap in the domestic market. In the second half of 2010, mass production was realized and the products were mainly exported. In 2011, some domestic OEMs began bulk orders.
The self-developed 900 N medium-sized vehicle gearbox has obvious advantages in the domestic market due to its large torque, multiple gear positions, fuel economy, and low price, and it has become one of the leading products supporting 2011 production and sales.
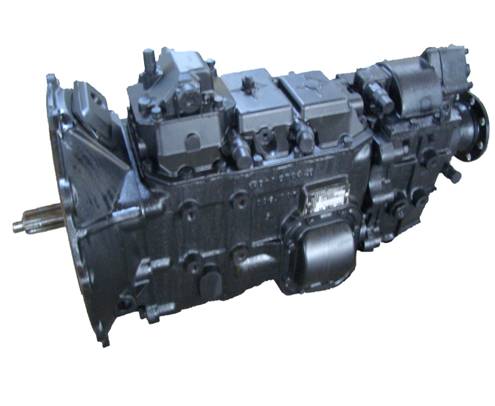
The 1500/1900 Nm double twin-shaft transmission is a new product introduced by Big Tooth into China National Heavy Duty Truck Group. In addition to supporting heavy-duty trucks, other markets are gradually increasing.
In order to cooperate with China National Heavy Duty Truck light truck project, Big Gear also developed 4 series of light vehicle gearboxes, some of which have already formed small batches to enter the road test stage. It is expected that the light vehicle gearbox will reach an annual output of 100,000 units by the end of 2011. ability.
Machining Brass
Brass has excellent CNC Machining Turning performance, high-speed machining turning under the brass can get excellent surface finish. Our technical team has very good experience in machining brass, machining brass including brass plate, brass rod, brass tube. Brass hardware parts has high strength, good plasticity in hot state, good plasticity in cold state, good machinability, easy welding and good corrosion resistance. Brass parts are very durable. It is electrically conductive and does not usually corrode or deteriorate over time. Thus brass is often used to produce products with longer service life. Machining brass parts Widely used: pipes, radiators, ship parts.
Machining Brass, Brass Machined Parts, Perfessional Brass Parts Machining, Machining Brass Conponents, Brass Parts Machining
Hong Kong RYH CO., LTD , https://www.szcncturning.com